Subaru Outback (BR): General Description of Heater, Ventilator, A/C
A: SPECIFICATION
1. HEATER SYSTEM
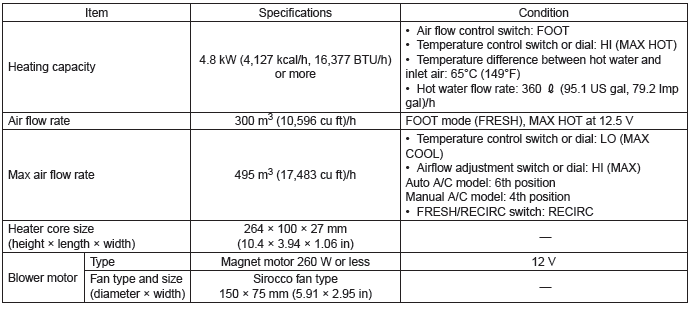
2. A/C SYSTEM
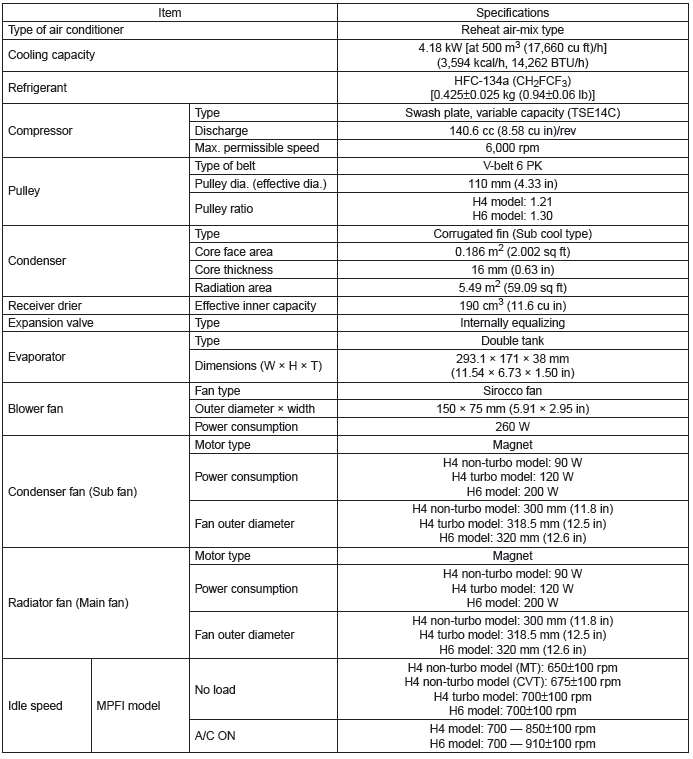
3. BASIC OPERATION
The cooling system cools down the compartment by using the pipes connecting parts and cycling the evaporable liquid (refrigerant) within the sealed system in a repeated process of "vaporization - liquefaction - re-vaporization".
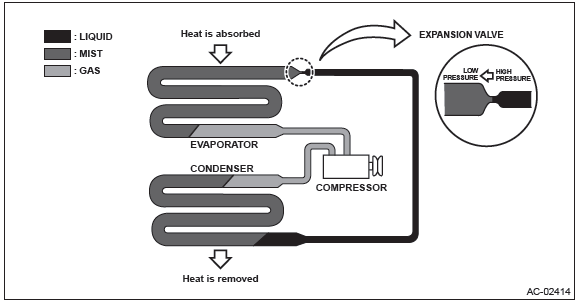
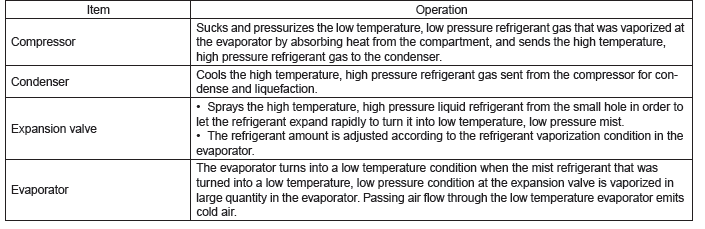
B: LOCATION
1. ELECTRICAL PARTS (ACTUATORS AND SENSORS)
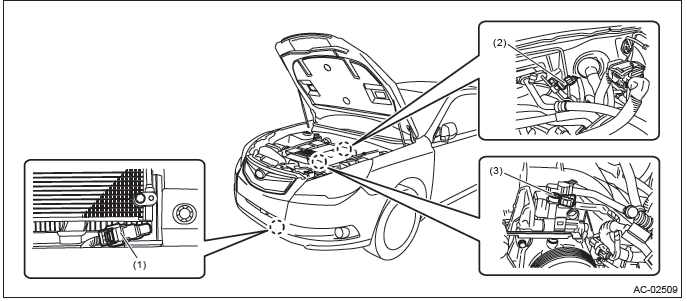
- Ambient sensor
- Pressure sensor
- Flow sensor
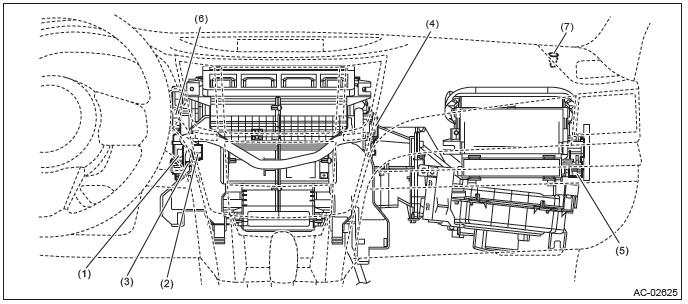
- Air mix door actuator (driver's seat)
- In-vehicle sensor
- Evaporator sensor
- Air mix door actuator (passenger's seat)
- Intake door actuator
- Mode door actuator
- Sunload sensor
C: COMPONENT
1. HEATER COOLING UNIT
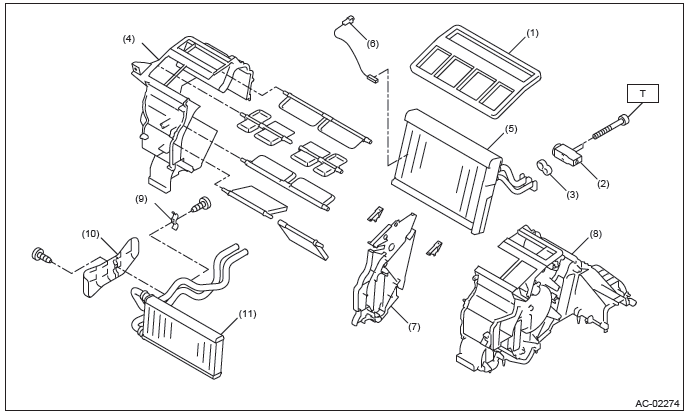
- Lining
- Expansion valve
- Gasket
- Heater case LH
- Evaporator
- Evaporator sensor
- Center plate
- Heater case RH
- Heater pipe clamp
- Heater pipe cover
- Heater core ASSY
Tightening torque: N*m (kgf-m, ft-lb)
T: 3.5 (0.36, 2.6)
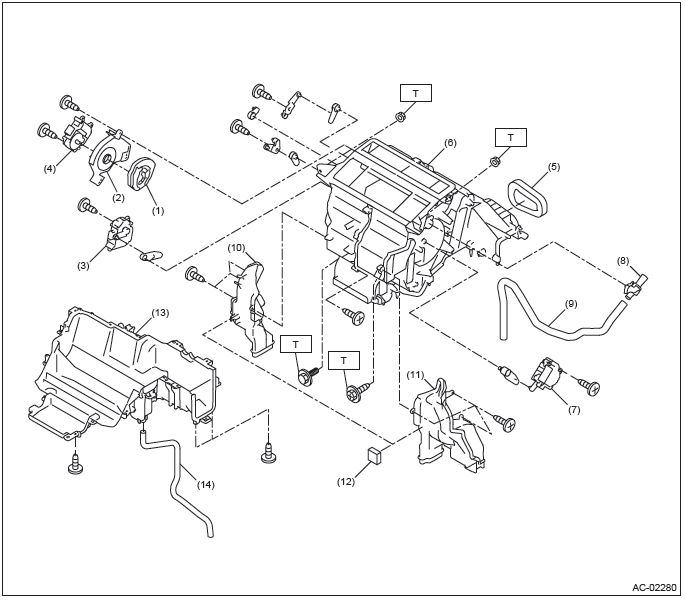
- Mode main lever
- Cover
- Air mix actuator (driver's seat)
- Mode actuator
- Gasket
- Unit ASSY
- Air mix actuator (passenger's seat)
- Aspirator
- Aspirator hose
- Foot duct LH
- Foot duct RH
- Gasket
- Heater case lower
- Drain hose
Tightening torque: N*m (kgf-m, ft-lb)
T: 7.5 (0.76, 5.5)
2. BLOWER MOTOR UNIT
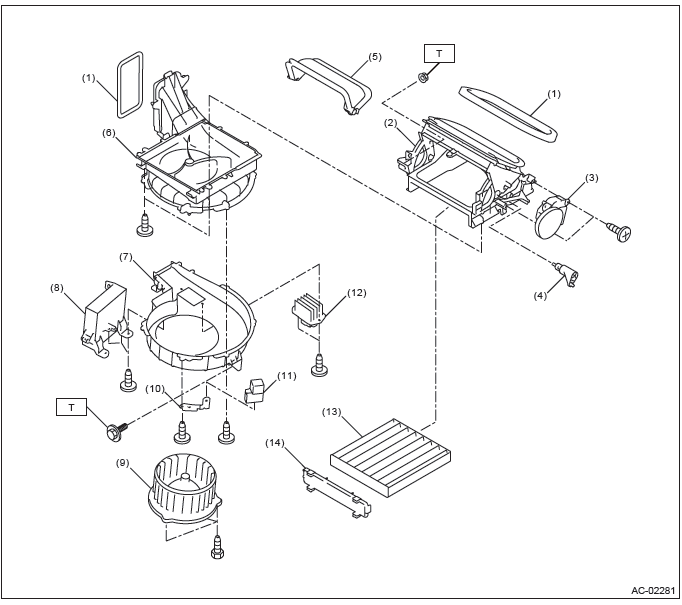
- Gasket
- Air duct cover ASSY
- Intake door actuator
- Intake door link
- FRESH/RECIRC door
- Upper case
- Lower case
- Control module
- Blower motor ASSY
- Relay holder bracket
- Blower motor relay
- Power transistor (auto A/C model) or resistor (manual A/C)
- Filter
- Filter cover
Tightening torque: N*m (kgf-m, ft-lb)
T: 7.5 (0.76, 5.5)
3. CONTROL MODULE

- Control module
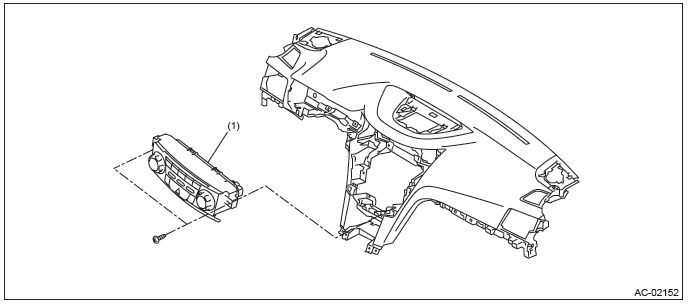
- Control module
4. AIR CONDITIONING UNIT
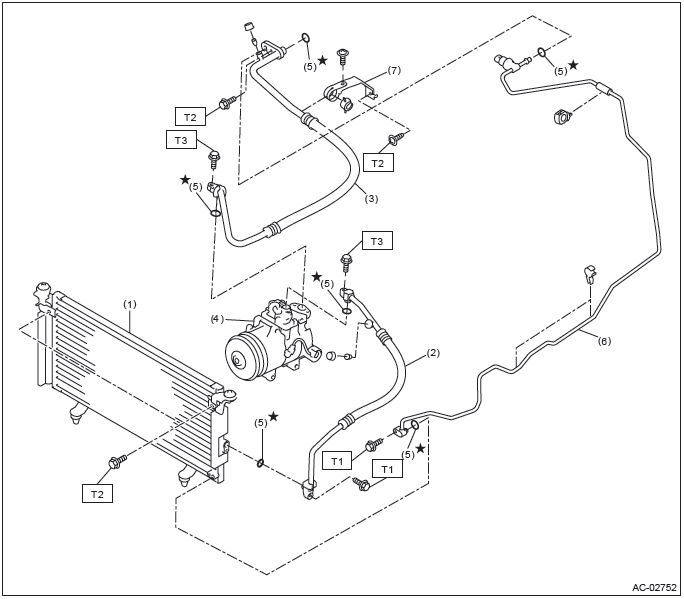
- Condenser
- Hose (high-pressure)
- Hose (low-pressure)
- Compressor
- O-ring
- Pipe
- Bracket
Tightening torque: N*m (kgf-m, ft-lb)
T1: 5 (0.51, 3.7)
T2: 7.5 (0.76, 5.5)
T3: 10 (1.02, 7.4)
5. COMPRESSOR
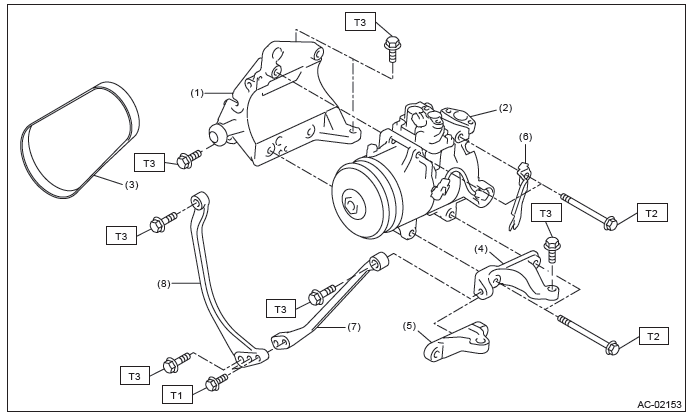
- A/C compressor stay
- Compressor
- V-belt (6 PK)
- Compressor bracket (H4 model)
- Compressor bracket (H6 model)
- Connector bracket
- Stopper rod LH (H4 model)
- Stopper rod RH (H4 model)
Tightening torque: N*m (kgf-m, ft-lb)
T1: 22 (2.24, 16.2)
T2: 26.5 (2.70, 19.5)
T3: 36 (3.67, 26.6)
6. HEATER DUCT
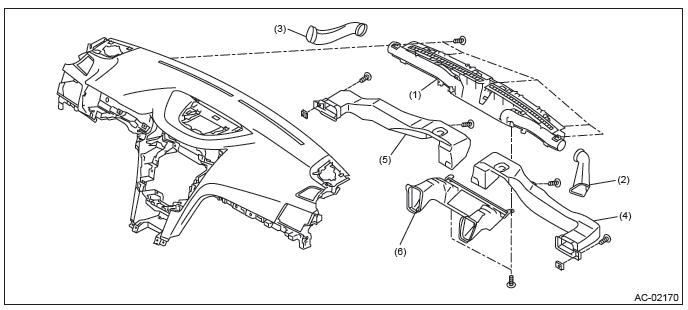
- Defroster nozzle ASSY
- Side defroster duct RH
- Side defroster duct LH
- Side vent duct RH
- Side vent duct LH
- Front vent duct
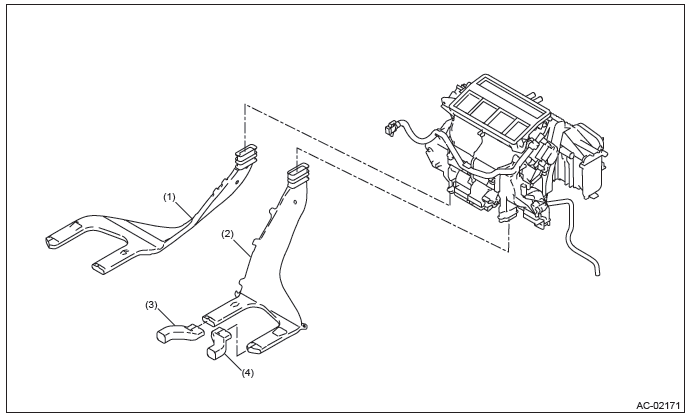
- Rear heater duct LH
- Rear heater duct RH
- Extension duct LH
- Extension duct RH
D: CAUTION
- Before disassembling or reassembling parts, always disconnect the battery ground cable from battery.
When replacing the radio, control module, and other parts provided with memory functions, record the memory contents before disconnecting the battery ground cable. Otherwise, the memory is cleared.
- Reassemble the parts in the reverse order of disassembly procedure unless otherwise indicated.
- Connect the connectors securely during reassembly.
- After reassembly, make sure that the functional parts operate normally.
1. HFC-134A A/C SYSTEM
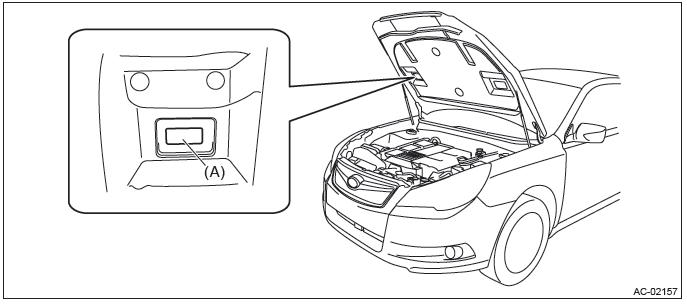
2. COMPRESSOR OIL
- HFC-134a compressor oil has no compatibility with that of CFC-12 system.
- Use only the manufacturer-authorized compressor oil, ND-OIL8, for the HFC-134a system.
- Do not mix multiple compressor oils.
If CFC-12 compressor oil is used in the HFC-134a A/C system, the compressor may become stuck due to poor lubrication, or the refrigerant may leak due to swelling of rubber parts.
On the other hand, if HFC-134a compressor oil is used in a CFC-12 A/C system, the durability of the A/C system will be lowered.
- HFC-134a compressor oil is very hygroscopic. When replacing or installing/removing A/C parts, immediately isolate the oil from atmosphere using a plug or tape. In order to avoid moisture, store the oil in a container with its cap tightly closed.
3. REFRIGERANT
- CFC-12 refrigerant cannot be used in a HFC-134a A/C system. HFC-134a refrigerant, also cannot be used in a CFC-12 A/C system.
- If an incorrect or no refrigerant is used, it will result in poor lubrication and the compressor itself may be damaged.
4. HANDLING OF REFRIGERANT
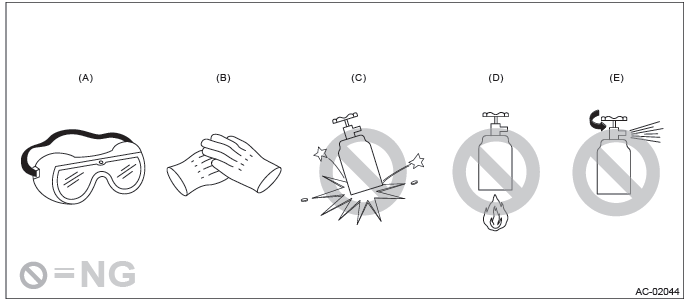
- Goggles
- Gloves
- Do not apply impact.
- No direct heat on container
- Do not discharge
5. O-RING CONNECTIONS
- Always use a new O-ring.
- In order to keep the O-rings free of lint which will cause a refrigerant gas leak, perform work without using gloves or waste cloths.
- Apply compressor oil to O-rings to avoid sticking, before installation.
- Use a torque wrench to tighten the O-ring fittings. Over-tightening will result in damage of the O-ring and deformation of the pipe end.
- If the work is interrupted before completing pipe connections, recap the pipes, components and fittings with a plug or tape to prevent foreign matter from entering.
- Visually check the surfaces and mating surfaces of O-rings, threads and connecting points. If a failure is found, replace the applicable parts.
- Install the O-rings straight against the pipe groove.
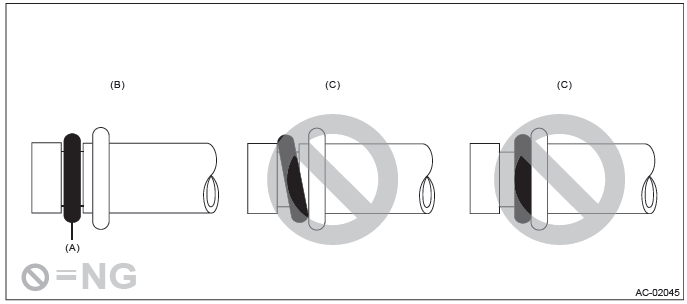
- O-ring
- OK
- NG
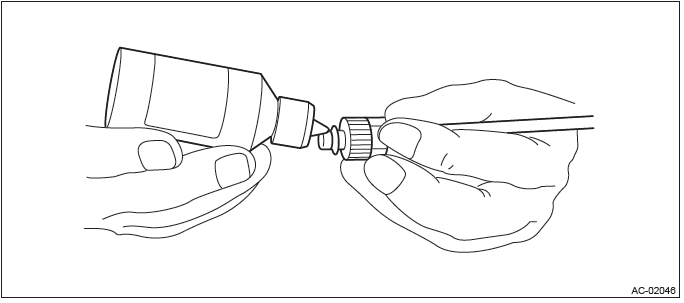
- After tightening, use a clean cloth to remove excess compressor oil from the connections and any oil which may have run on the vehicle body or other parts.
- If any leakage is suspected after tightening, do not tighten the connections further, but disconnect the connections, remove the O-rings, and check the O-rings, threads, and connections.
E: PREPARATION TOOL
1. SPECIAL TOOL
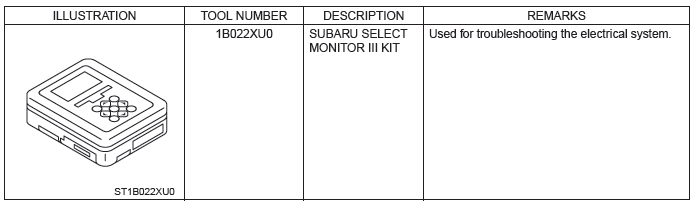
2. GENERAL TOOL
CAUTION: When working on vehicles with a HFC-134a system, only use HFC-134a specified tools and parts. Do not mix CFC-12 tools and parts. If HFC-134a and CFC-12 refrigerant or compressor oil is mixed, it will result in poor lubrication and the compressor itself may be damaged.
In order to prevent the mixture of HFC-134a and CFC-12 parts and liquid, the type of tool and screw, and the replacement valves used are different. The gas leak detectors for the HFC-134a and CFC-12 systems must also not be interchanged.
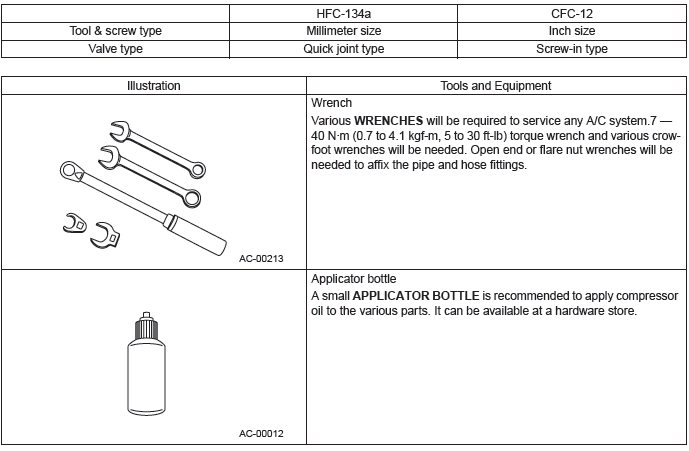
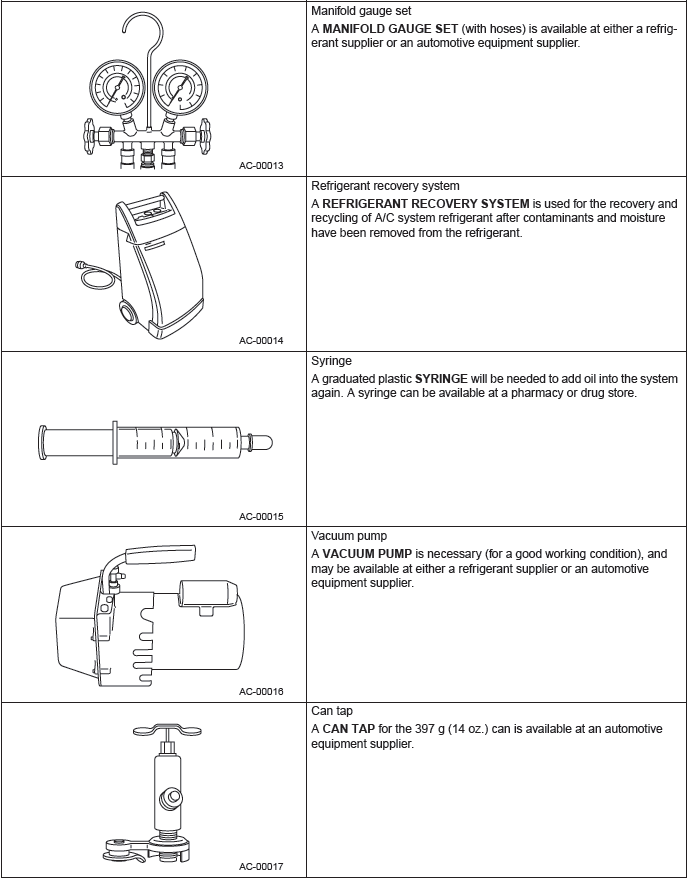
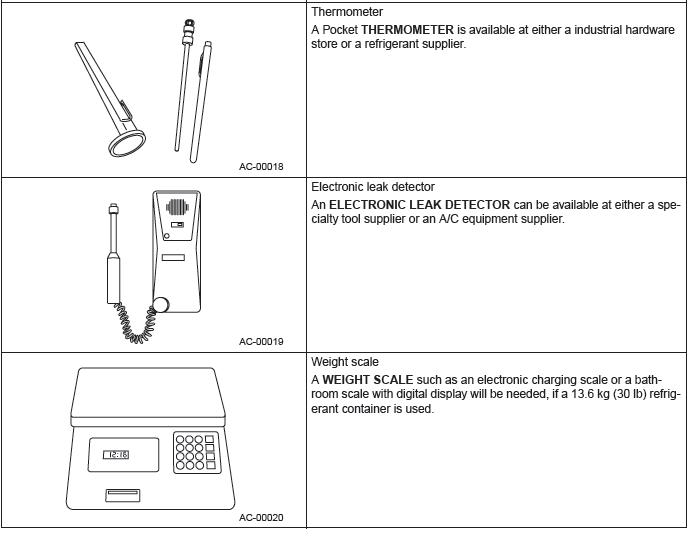
READ NEXT:
A: WIRING DIAGRAM
Refer to "Air Conditioning System" in the wiring diagram. <Ref. to WI-53,
WIRING DIAGRAM, Air Conditioning
System.>
B: ELECTRICAL SPECIFICATION
Refer to "Auto A/C Control Modu
A: LOCATION
NOTE: For other related fuses, refer to the wiring diagram. <Ref. to WI-15, Power Supply Circuit.>
B: INSPECTION
1. CHECK FUSE.
1) Remove the fuse and inspect visually.
2) If
A: REMOVAL
1) Disconnect the ground cable from battery.
2) Using the refrigerant recovery system, discharge refrigerant. <Ref. to AC-24,
PROCEDURE, Refrigerant
Recovery Procedure.>
3) Drain t
SEE MORE:
1) U.S.-spec. models
2) Except U.S.-spec. models
The driving range indicates the distance that can be driven taking into account
the amount of fuel remaining in the tank and the average rate of fuel consumption.
When the low fuel warning light illuminates, the driving range indication flashe
The fuel tank's low fuel warning light activates when it's nearly empty and only functions with the ignition switch in the "ON" position. When this light comes on, it's crucial to refill the fuel tank promptly.
Please be cautious and refill the tank as soon as the low fuel warning light a
© 2010-2025 Copyright www.suoutback.com
